Copper Extrusion Press
A copper extrusion machine is a kind of equipment used to extrude copper tubes and copper alloy tubes, rods, rows, wires, and other products.
Photos of
Detailed introduction
Dalian Jiuying Machinery Equipment Co., Ltd., established in 2015, is a professional company dedicated to the research, production, and sales of high-quality copper extrusion machines. Adhering to the principles of innovation, quality, and superior service, we provide efficient, durable, and precise machinery to meet the diverse needs of our customers across various applications. Over the years, our products have been widely used in domestic and international markets, earning the trust of our users. Dalian Jiuying Machinery Equipment Co., Ltd. will continue to focus on technological advancement and product optimization, striving to maintain a leading position in the copper extrusion machine industry.
Why Choose Us
01|Expertise and Experience
With nearly a decade of experience since our establishment in 2015, Dalian Jiuying Machinery Equipment Co., Ltd. has developed extensive expertise in the copper extrusion machine industry. Our team of skilled engineers and technicians are dedicated to providing the best solutions for our customers.
02|Price advQuality Assuranceantage
We prioritize quality in every aspect of our production process. Our copper extrusion machines are manufactured using high-grade materials and undergo rigorous testing to ensure durability, precision, and high performance.
03|Customer-Centric Approach
At Dalian Jiuying Machinery Equipment Co., Ltd., customer satisfaction is our top priority. We offer personalized service, tailor-made solutions, and responsive support to address the unique needs of each client.
Product description
Description
Our copper extrusion machines are designed to produce high-quality copper profiles with precision and efficiency. These machines heat copper alloy billets and apply high pressure to extrude them through a die, creating various shapes of copper products.
Key features include
High Precision: Ensures accurate shaping of copper profiles.
High Efficiency: Optimized for rapid production rates.
Durability: Built with robust materials to withstand continuous industrial use.
Versatility: Capable of handling various copper alloys and profile shapes.
Energy Efficient: Designed to minimize energy consumption while maintaining top performance.
For more information, visit our official website.
Features
Touch Screen-Mitsubishi
1.User-friendly interface
2.Durability
3.Advanced features
4.TEYUN's control program
Electrical Appliance-Schneider
1.High security
2.High switching fexibiloty
3.Low failure rate
4. Energy saving
5. Environmental protection
Pump-Rexroth
1.Efficient
2.Long life
3.Good Sealing
4.Vriable Convenience
Valve Block-Rexroth
1.High working reliability
2.Low fluid resistance
3.Excellent inhalation ability
4.High sensitivity
PLC-Mitsubishi
1.Powerful
2.High reliability
3.High stability
MOTOR-Chinese Famous
1.High working efficiency
2.Long life
3.Low failure rate
4.Run smoothly
Contact Us
Thank you for your interest in Dalian Jiuying Machinery Equipment Co., Ltd. We are here to assist you with any questions or inquiries you may have regarding our products and services.
Whatsapp/Mob/Wechat: 008613394110095
Email: [email protected]
Website: www.aluextrusionpress.com
Working Principle
A copper extrusion machine operates by heating copper alloy billets to the appropriate temperature and applying high pressure to push them through a die, producing various shapes of copper profiles. Below are the main steps involved in the working principle of a copper extrusion machine:
1. Pre-treatment
First, the copper alloy billets undergo pre-treatment, including cleaning and heating. The billets are typically heated to a temperature of 700-800°C, making the copper alloy more malleable and easier to extrude.
2. Loading into the Extrusion Cylinder
The preheated billets are then loaded into the extrusion cylinder. The extrusion cylinder is a high-strength, cylindrical container designed to withstand high temperatures and pressures.
3. Extrusion Process
A hydraulic ram applies immense pressure (usually between 50-150 MPa) to the billet, pushing it towards the die. Under pressure, the copper alloy is forced through the die, forming a continuous copper profile. The shape of the die determines the cross-sectional shape of the final extruded product.
4. Cooling
The extruded copper profiles typically pass through a cooling process to solidify and retain their shape. Cooling can be done using air or water quenching, depending on the specific requirements of the profile.
5. Cutting and Finishing
Once cooled, the continuous copper profiles are cut to the desired lengths. Further finishing processes, such as stretching, straightening, and aging, may be applied to enhance the mechanical properties and surface finish of the profiles.
Main Application Scenarios
Our copper extrusion machines find extensive application in various industries where precision-crafted copper profiles are essential. Here are some of the main application scenarios:
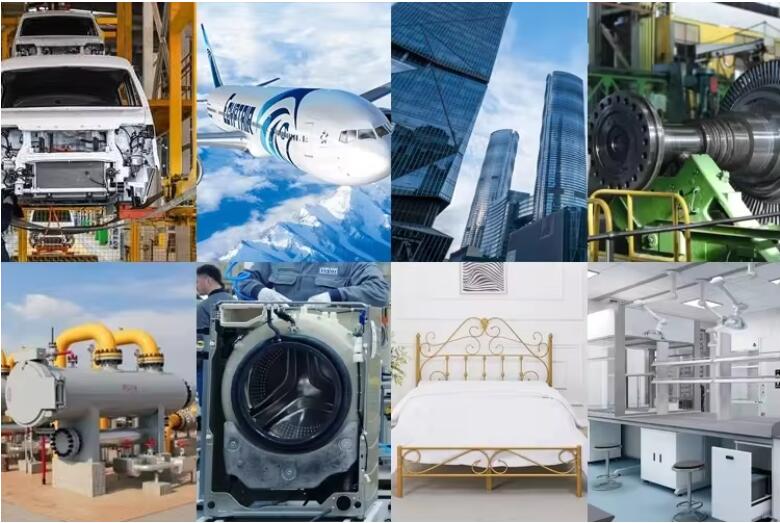
Electrical Industry
Cable Conductors:
Producing high-conductivity copper wires and cables for electrical transmission.
Busbars:
Manufacturing copper busbars for power distribution and electrical equipment.
Automotive Sector
Heat Exchangers:
Creating copper tubes and fins for automotive radiators and air conditioning systems.
Electrical Components:
Fabricating copper connectors and terminals for automotive electronics.
Consumer Electronics
Heat Sinks:
Producing copper heat sinks for electronic devices to dissipate heat efficiently.
Connectors:
Manufacturing precision copper connectors and pins for electronic circuits.
Industrial Machinery
Hydraulic Systems:
Crafting copper tubes and fittings for hydraulic systems in industrial machinery.
Pump Components:
Producing copper impellers and casings for pumps and compressors.
Renewable Energy
Solar Panels:
Manufacturing copper frames and components for solar panel installations.
Wind Turbines:
Crafting copper conductors and connectors for wind turbine generators.
Aerospace and Aviation
Heat Management:
Fabricating copper heat exchangers and thermal management systems for aircraft.
Electrical Wiring:
Producing lightweight copper wires and harnesses for aerospace applications.
These are just a few examples of the diverse applications of our copper extrusion machines. Whether it's for electrical conductivity, thermal efficiency, or structural integrity, our machines deliver precision-crafted copper profiles to meet the stringent demands of various industries.
Product Parameters
Model | Unit | JY-630 | JY-800 | JY-1000 | JY-1250 | JY-1630 | JY-1800 | JY-2200 | JY-2500 |
Rated Extrusion Force | KN | 6300 | 8000 | 10000 | 12500 | 16300 | 18000 | 22000 | 25000 |
UST | 700 | 880 | 1100 | 1350 | 1800 | 2000 | 2420 | 2750 | |
Fixed Work Stress | MPa | 21 | 21 | 21 | 21 | 21 | 21 | 21 | 21 |
Locking Force | KN | 633 | 633 | 800 | 800 | 1586 | 1586 | 1586 | 1586 |
Perforation Force (Double Action Extrusion Machine) | KN | 1030 | 1030 | 1293 | 1293 | 2500 | 2800 | 3000 | 3500 |
Extruding Speed | mm/s | 40 | 50 | 40 | 50 | 40 | 40 | 40 | 40 |
Extrusion Cylinder Preheating Power (Single Per Rod × Number) | KW | 1.2×12 | 1.5×12 | 2×12 | 2×12 | 3×12 | 3×12 | 3×15 | 3.5×15 |
Main Motor Power | KW | 75×3 | 132×3 | 132×3 | 132×4 | 132×5 | 132×6 | 132×7 | 132×8 |
Extrusion Barrel Inner Hole Size Range (Aperture x Length) | mm | φ85-φ115×500 | φ105-φ135×550 | φ125-φ135×600 | φ135-φ165×650 | φ155-φ205×750 | φ175-φ225×800 | φ195-φ245×900 | φ205-φ265×1000 |
Center Height of Main Unit | mm | 850 | 1040 | 1100 | 1180 | 1500 | 1500 | 1650 | 1850 |
Dimensions of Single-action Host (L × W × H) | m | 6.8×2.3×2.8 | 9.2×2.3×3.1 | 10×2.4×3.3 | 11.5×2.5×3.4 | 13.5×4.2×4.1 | 14.5×4.2×4.1 | 15.5×4.7×4.5 | 18×5×4.8 |
Dimensions of Dual-action Host (length × width × height) | m | 7.8×2.3×2.8 | 10.5×2.3×3.1 | 11.8×2.4×3.3 | 13.3×2.5×3.4 | 15.5×4.2×4.1 | 16.5×4.2×4.1 | 18.5×4.7×4.5 | 20×5×4.8 |
Similar products
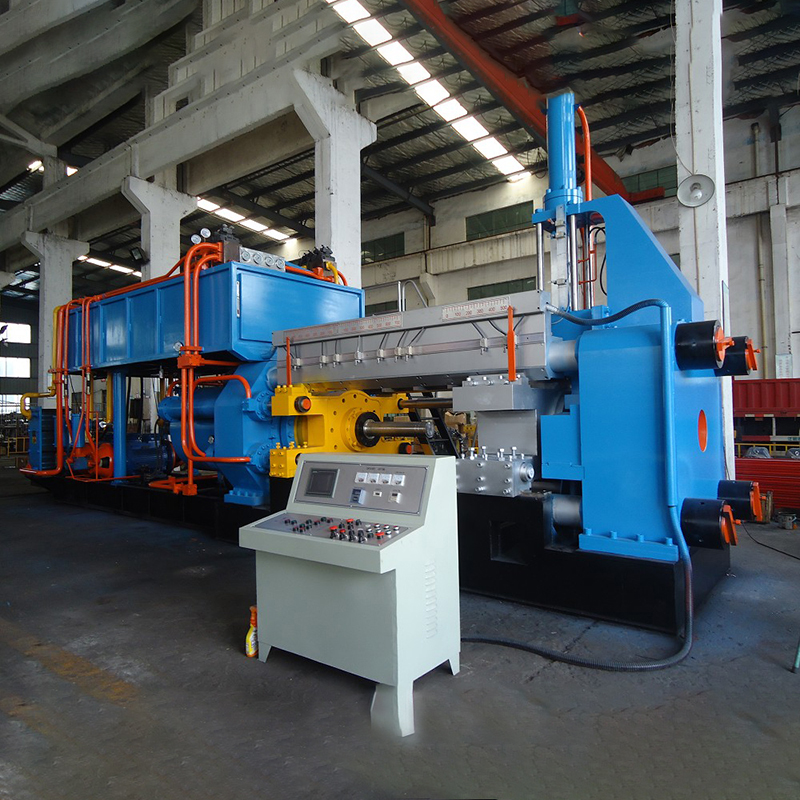
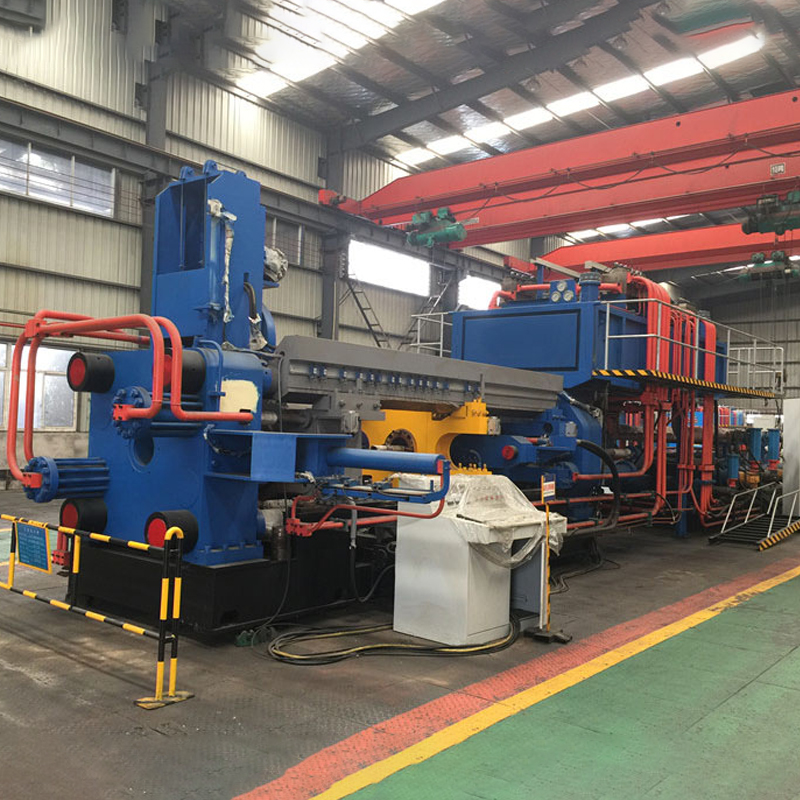
How to Enquire
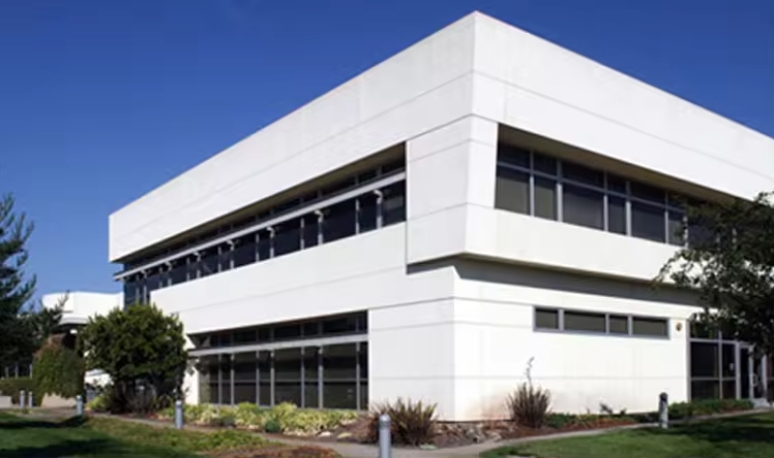
Dalian Jiuying Machinery Equipment Co., Ltd. is a leading manufacturer specializing in the research, development, and production of high-quality extrusion machinery. Since our establishment in 2015, we have been committed to providing innovative solutions and exceptional service to our customers worldwide.
Our Mission
At Dalian Jiuying Machinery Equipment Co., Ltd., our mission is to deliver advanced extrusion technology that empowers our customers to excel in their industries.
We strive to:
Innovate: Continuously develop cutting-edge extrusion machinery to meet evolving market needs.
Quality: Ensure the highest standards of quality and precision in every machine we produce.
Customer Satisfaction: Provide personalized service and support to exceed our customers' expectations.
Sustainability: Embrace environmentally friendly practices in our manufacturing processes.

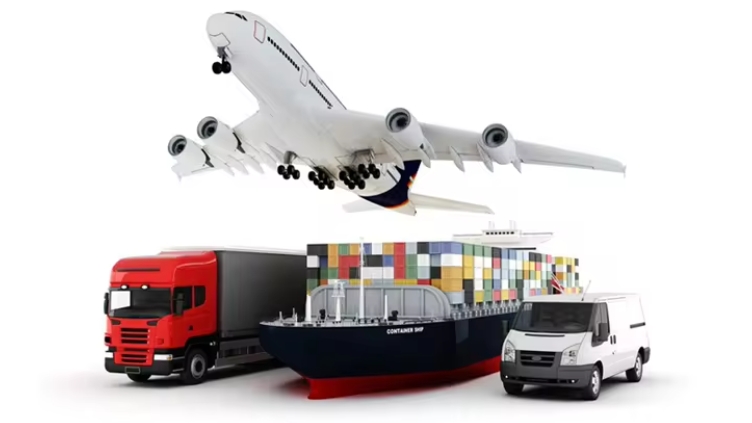
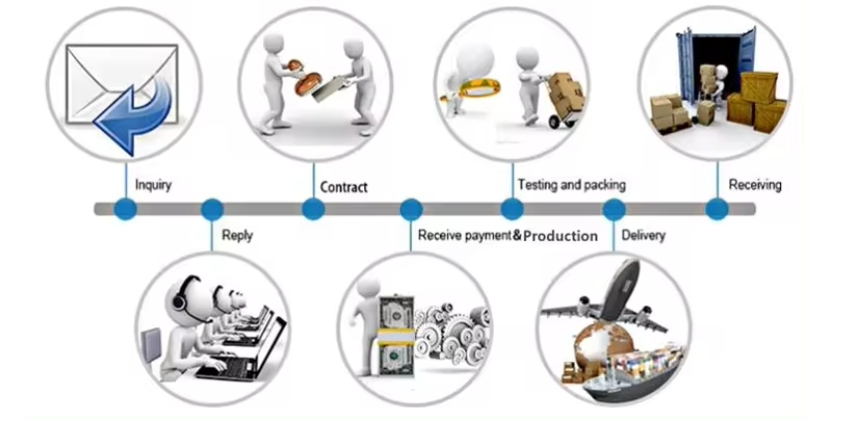
Whatsapp/Mob/Wechat: 008613394110095
Email: [email protected]
Website: www.aluextrusionpress.com
Common Issues and Solutions
At Dalian Jiuying Machinery Equipment Co., Ltd., we understand that our customers may encounter various challenges while operating their extrusion machines. Here are some common issues and their solutions:
1. Uneven Extrusion
Issue: The extruded product has uneven dimensions or surface quality.
Solution:
- Check for alignment issues in the die or extrusion cylinder.
- Ensure consistent temperature and pressure throughout the extrusion process.
- Inspect the billet for defects or irregularities before loading into the machine.
2. Extrusion Defects
Issue: Defects such as surface roughness, cracking, or warping occur in the extruded product.
Solution:
- Optimize die design and surface finish to minimize defects.
- Control temperature and speed parameters to prevent overheating or rapid cooling.
- Use high-quality billets with uniform composition and microstructure.
3. Machine Downtime
Issue: Unexpected downtime due to mechanical failures or maintenance issues.
Solution:
- Implement a regular maintenance schedule to prevent breakdowns.
- Keep spare parts on hand for quick replacements when needed.
- Train operators on proper machine operation and maintenance procedures.
4. Material Waste
Issue: Excessive material waste during the extrusion process.
Solution:
- Fine-tune process parameters to minimize material loss.
- Implement recycling programs to reuse scrap material.
- Optimize billet size and shape to reduce waste during machining.
5. Product Quality Control
Issue: Inconsistent product quality or non-compliance with specifications.
Solution:
- Implement quality control measures at every stage of the production process.
- Use advanced inspection techniques, such as dimensional analysis and surface testing.
- Regularly calibrate equipment and tools to maintain accuracy.
6. Energy Consumption
Issue: High energy consumption leading to increased operating costs.
Solution:
- Invest in energy-efficient equipment and technologies.
- Optimize process parameters to minimize energy usage without compromising productivity.
- Implement energy management systems to monitor and control consumption.
Contact Us for Assistance
If you encounter any of these issues or have other concerns regarding your extrusion machine, please don't hesitate to contact our customer support team. We are here to help you troubleshoot problems, provide technical assistance, and ensure the optimal performance of your equipment.
Copper Extrusion Press Machine Maintenance
Proper maintenance of your copper extrusion press machine is essential to ensure its longevity, efficiency, and safety. Here are some key maintenance tasks:
1. Regular Cleaning and Lubrication
- Cleaning: Regularly clean the machine's components, including the extrusion cylinder, die, and hydraulic system, to remove dirt, debris, and metal shavings.
- Lubrication: Ensure all moving parts are properly lubricated to reduce friction and prevent premature wear. Use recommended lubricants and follow the manufacturer's guidelines.
2. Inspection of Wear Parts
- Regularly inspect wear parts such as seals, gaskets, and bearings for signs of damage or wear. Replace any worn-out components promptly to prevent leaks or breakdowns.
3. Hydraulic System Maintenance
- Check hydraulic fluid levels regularly and top up as needed. Inspect hydraulic hoses and fittings for leaks or damage, and replace them if necessary.
- Monitor hydraulic pressure and temperature to ensure they are within recommended ranges during operation.
4. Die and Tooling Maintenance
- Inspect the die for signs of wear, damage, or buildup of contaminants. Clean or replace the die as needed to maintain product quality.
- Check tooling components such as punches, mandrels, and guides for wear and alignment issues. Adjust or replace them as necessary for proper extrusion.
5. Electrical and Control System Checks
- Inspect electrical wiring, connections, and control panels for signs of damage or loose connections. Ensure all safety devices and emergency stops are functioning correctly.
- Regularly calibrate sensors, gauges, and controllers to maintain accurate process control.
6. Operator Training and Safety
- Provide regular training for machine operators on proper operation, maintenance procedures, and safety protocols.
- Ensure operators wear appropriate personal protective equipment (PPE) and follow safety guidelines to prevent accidents and injuries.
7. Scheduled Maintenance Plan
- Develop a scheduled maintenance plan outlining routine maintenance tasks and intervals based on machine usage and manufacturer recommendations.
- Keep detailed records of maintenance activities, including inspections, repairs, and replacements.
Contact Professional Support
- For complex maintenance tasks or troubleshooting issues, consider consulting with qualified technicians or contacting the machine manufacturer for professional support.
By following these maintenance guidelines and implementing a proactive approach to machine care, you can maximize the performance and reliability of your copper extrusion press machine.
Frequently Asked Questions (FAQ) for Copper Extrusion Press
What is a copper extrusion press machine, and how does it work?
A: A copper extrusion press machine is a type of equipment used to shape copper alloy billets into various profiles through the application of heat and pressure. It works by heating the billet to a specific temperature, then applying high pressure to push it through a die, resulting in the desired shape.What are the main applications of copper extrusion press machines?
A: Copper extrusion press machines are commonly used in industries such as electrical, automotive, construction, and consumer electronics for producing copper profiles used in cables, heat exchangers, piping systems, and electrical components.What factors should be considered when selecting a copper extrusion press machine?
A: Factors to consider include production capacity, extrusion force, die size and design, material compatibility, energy efficiency, and maintenance requirements.How can I ensure the quality of extruded copper profiles?
A: Quality assurance measures include maintaining consistent process parameters (temperature, pressure, speed), using high-quality billets, inspecting dies and tooling regularly, and implementing a comprehensive quality control system.What are the common maintenance tasks for copper extrusion press machines?
A: Common maintenance tasks include cleaning and lubrication, inspection of wear parts, maintenance of the hydraulic system, die and tooling maintenance, electrical system checks, operator training, and adherence to a scheduled maintenance plan.How can I troubleshoot common issues with my copper extrusion press machine?
A: Troubleshooting steps may include identifying and addressing issues such as uneven extrusion, extrusion defects, machine downtime, material waste, product quality control, and energy consumption. Regular inspection, proper maintenance, and operator training are key to preventing and resolving issues.What safety precautions should be followed when operating a copper extrusion press machine?
A: Safety precautions include wearing appropriate personal protective equipment (PPE), following safety guidelines and procedures, ensuring proper machine guarding, providing operator training, and conducting regular safety inspections.How can I optimize the performance and efficiency of my copper extrusion press machine?
A: Performance optimization strategies include optimizing process parameters, implementing energy-saving technologies, upgrading to advanced control systems, investing in quality tooling and dies, and conducting regular performance assessments.What are the environmental considerations associated with copper extrusion press machines?
A: Environmental considerations include managing waste materials and emissions, implementing recycling programs for scrap material, optimizing energy usage, and complying with environmental regulations and standards.Where can I find additional resources and support for my copper extrusion press machine?
A: Additional resources and support may be available from the machine manufacturer, industry associations, online forums, and technical publications. Professional technicians and consultants can also provide specialized assistance as needed.Can copper extrusion press machines handle different types of copper alloys?
A: Yes, copper extrusion press machines are designed to handle various types of copper alloys, including pure copper, brass, bronze, and copper-nickel alloys. Different alloys may require adjustments to process parameters such as temperature and pressure.What is the typical lifespan of a copper extrusion press machine?
A: The lifespan of a copper extrusion press machine depends on factors such as usage, maintenance, and the quality of components. With proper care and maintenance, a well-built machine can last for several decades.Can copper extrusion press machines be customized to suit specific production requirements?
A: Yes, many manufacturers offer customization options to tailor the machine to specific production needs. Customization may include die design, extrusion force, cooling systems, automation features, and control systems.What training is available for operators of copper extrusion press machines?
A: Manufacturers often provide training programs for machine operators, covering topics such as machine operation, maintenance procedures, safety protocols, and troubleshooting techniques. Training can be conducted onsite or at the manufacturer's facility.How do I determine the appropriate size of a copper extrusion press machine for my production needs?
A: Factors to consider when sizing a machine include the desired production capacity, the size and complexity of the extruded profiles, and the available floor space. Manufacturers can provide guidance based on specific requirements.Can copper extrusion press machines be integrated into existing production lines?
A: Yes, copper extrusion press machines can be integrated into existing production lines with proper planning and coordination. Manufacturers can work with customers to design seamless integration solutions.What are the advantages of using copper extrusion press machines over other manufacturing methods?
A: Copper extrusion press machines offer advantages such as high production efficiency, precise control over product dimensions, minimal material waste, and the ability to produce complex shapes with excellent surface finish.Are there any safety certifications or standards that copper extrusion press machines should adhere to?
A: Manufacturers should adhere to relevant safety standards and regulations, such as ISO 9001 for quality management and ISO 14001 for environmental management. Additionally, machines may need to comply with safety standards specific to the industry or region.Can copper extrusion press machines be retrofitted with new technology or upgrades?
A: Yes, many manufacturers offer retrofitting services to upgrade existing machines with new technology, automation features, control systems, or safety enhancements. Retrofitting can improve performance, efficiency, and safety.What are the typical lead times for ordering and receiving a copper extrusion press machine?
A: Lead times can vary depending on factors such as customization requirements, production capacity, and supplier availability. Manufacturers can provide estimated lead times based on specific project details.