Photos of
Detailed introduction
About Us
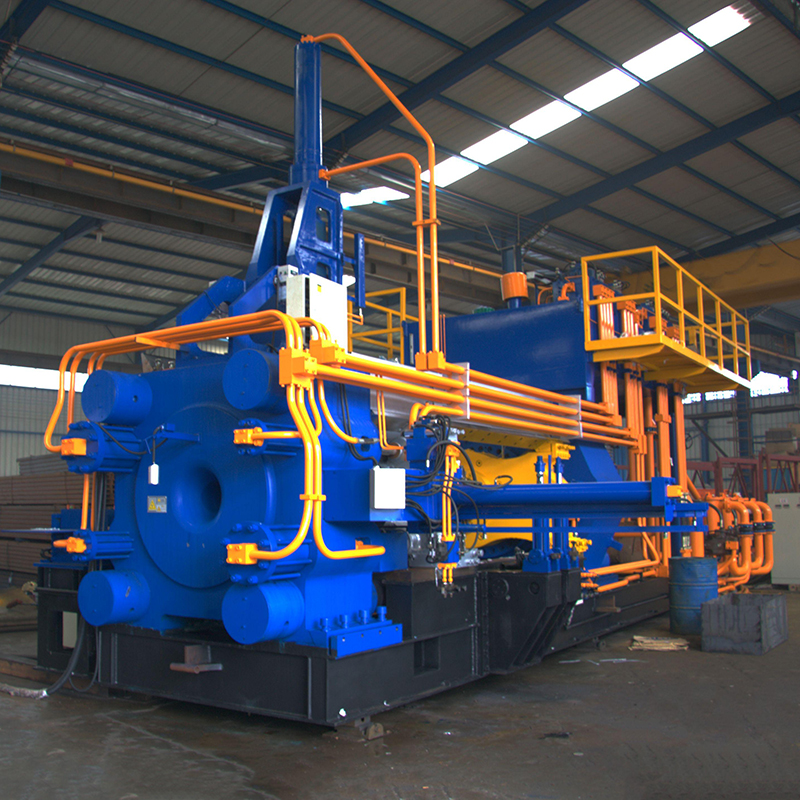
Established in 2015, Dalian Jiuying Machinery Equipment Co., Ltd. specializes in advanced extrusion equipment for aluminum and copper profiles, serving industries such as automotive, aerospace, and construction. With strong R&D and customization capabilities, our high-performance extruders are trusted worldwide, including in the US, Italy, and Russia. Committed to innovation and customer satisfaction, we strive for long-term, win-win partnerships. Choose Jiuying for your extrusion solutions.
01|Advanced Technology
Our state-of-the-art extrusion equipment ensures high performance and reliability, catering to diverse industries including automotive, aerospace, and construction.
02|Global Trust
The operation panel features manual, semi-automatic, and automatic settings, reflecting a humanized design concept that prioritizes user-friendliness and ease of operation.
03|Customized Solutions
We offer robust R&D and product development capabilities, providing tailored production services to meet the unique needs of each customer.
Introduction
Aluminium extrusion fabrication is a pivotal process in the manufacturing industry, offering versatile solutions for shaping aluminium into various profiles for a myriad of applications. At the heart of this process lies the aluminium extrusion press, a sophisticated machine meticulously engineered to transform raw aluminium into precise, custom profiles.
Working Principle
The working principle of an aluminium extrusion press is elegantly simple yet remarkably efficient. It operates by forcing molten aluminium through a shaped die, thereby creating the desired profile. This process is facilitated by immense pressure generated within the press, typically through hydraulic systems, ensuring accurate and consistent results.
Features
Host Part
Crafted from high-quality cast steel or forged steel, the main components such as the main cylinder and front beam ensure robustness and durability, withstanding the rigors of heavy-duty operation.
Host Part
Crafted from high-quality cast steel or forged steel, the main components such as the main cylinder and front beam ensure robustness and durability, withstanding the rigors of heavy-duty operation.
Host Part
The main plunger, meticulously made from chilled cast iron, features a surface plated with hard chrome, finely ground to minimize roughness, thereby ensuring smooth and precise extrusion.
Host Part
Utilizing 45# steel, the tension column undergoes rigorous flaw detection processes to guarantee structural integrity, providing a stable foundation for the extrusion process.
Host Part
The ingeniously inverted oil cylinder of the shearing mechanism offers stability and prolonged durability, enhancing the overall reliability of the machine.
Host Part
Designed for convenience, the die change cylinder adopts a direct push type design, facilitating seamless operation and maintenance procedures, minimizing downtime.
Host Part
With adjustable stroke capabilities, the locking cylinder proves versatile, capable of extruding seamless aluminum tubes of varying lengths with precision.
Host Part
Special quenching processes applied to the extrusion rod and barrel effectively extend the lifespan of extrusion tools, ensuring consistent quality over prolonged usage.
Host Part
Host Part:Featuring an external spindle cylinder, the machine ensures stability and reliability, critical for achieving precise extrusion results.
Host Part
A flat guide rail structure, coupled with adjustable movable beam centers, simplifies the calibration machine's extrusion center adjustment, enhancing operational efficiency.
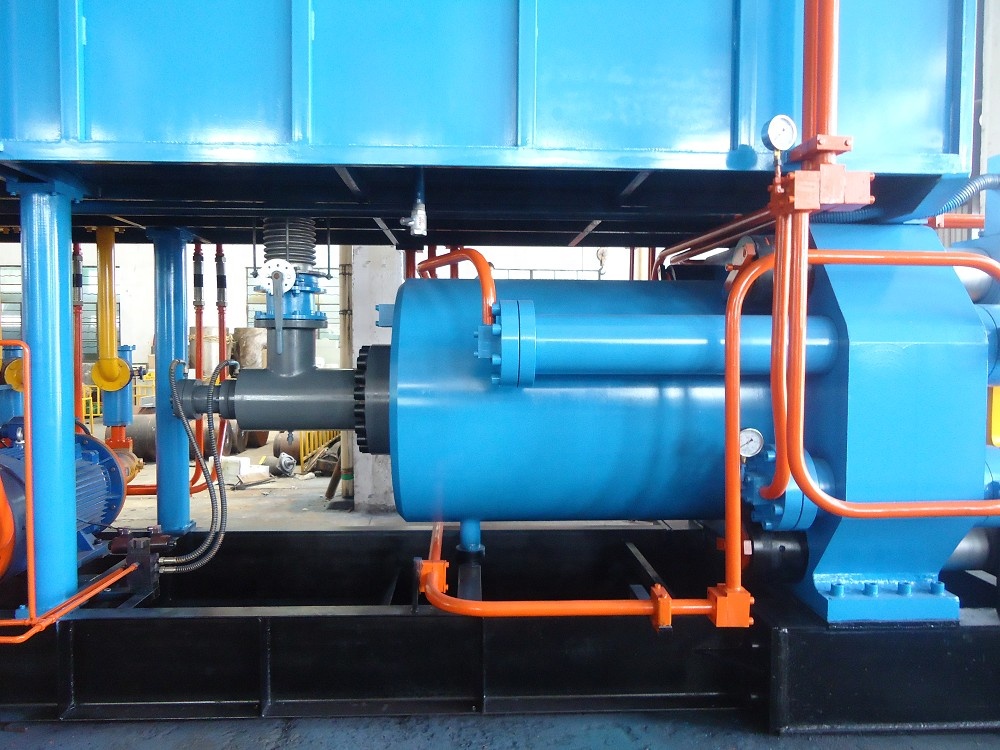
Hydraulic Part
The hydraulic system adopts a high and low-pressure configuration, differentially connected for fast response and stable action, thereby extending the main valve's service life and ensuring consistent performance.
Hydraulic Part
Hydraulic systems for machines of 1250T and above are categorized into traditional slide valve control systems and disassembly and assembly valve systems (VC valve system), offering users flexibility based on specific requirements and process demands.
Hydraulic Part
Proportional valves and servo valves can be integrated to enable the system to regulate speed, pressure, and facilitate constant speed extrusion, providing versatility to accommodate a wide range of extrusion processes.
Hydraulic Part
Imported seals are employed in the high-pressure section, minimizing oil leakage and ensuring the reliability and longevity of the hydraulic system.
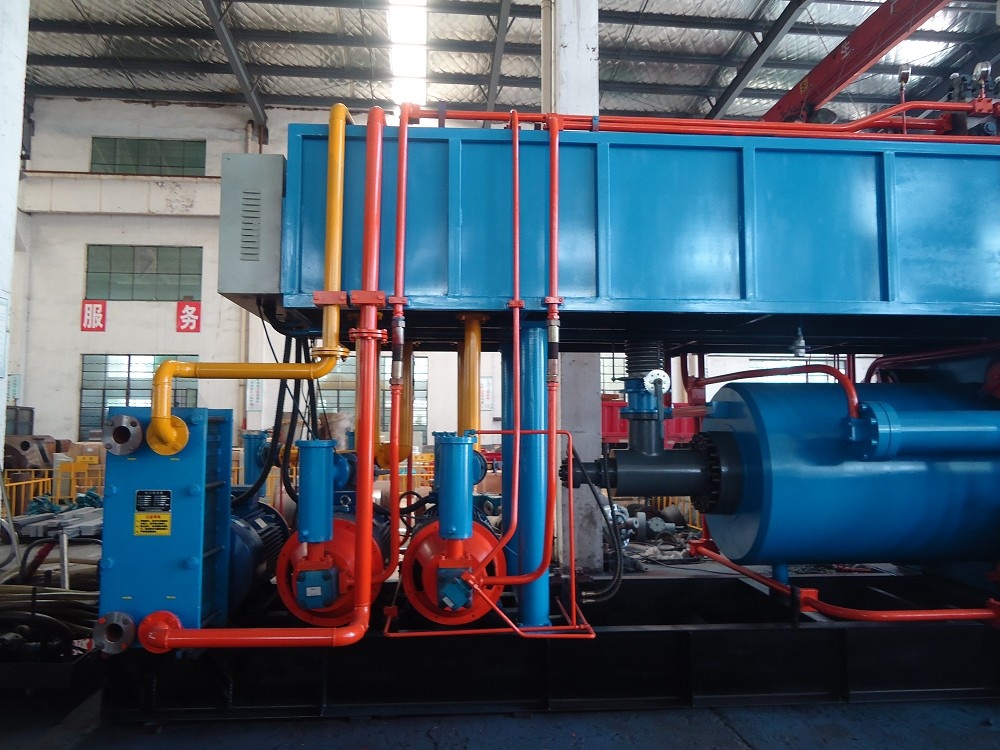
Electronic Control Part
The main motor adopts a 6-pole horizontal structure, significantly extending the pump's service life, reducing maintenance requirements, and enhancing operational efficiency.
Electronic Control Part
Imported programmable controllers (PLCs) govern the operation, ensuring precision and reliability in controlling the extrusion process, minimizing errors and maximizing productivity.
Electronic Control Part
The operation panel features manual, semi-automatic, and automatic settings, reflecting a humanized design concept that prioritizes user-friendliness and ease of operation.
Electronic Control Part
Key components of both strong and weak electricity utilize imported parts, ensuring reliability and longevity, critical for maintaining uninterrupted production processes.
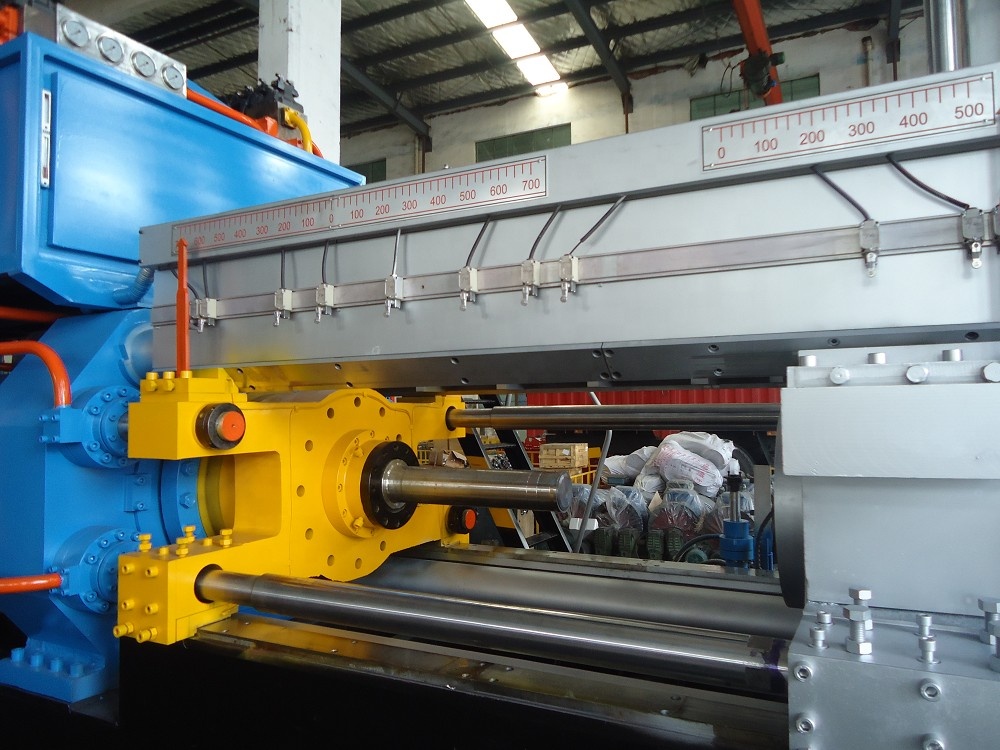
Contact Us
Ready to revolutionize your aluminum extrusion capabilities? Contact us today to explore how our advanced aluminum profile extrusion line machines can elevate your manufacturing processes. Our team of experts is poised to assist you in selecting the perfect solution tailored to your specific requirements. Don't miss out on the opportunity to unlock unparalleled efficiency and precision in aluminum profile extrusion—reach out to us now!
Whatsapp/Mob/Wechat: 008613394110095
Email: [email protected]
Website: www.aluextrusionpress.com
Beyond the exceptional features highlighted above, our aluminum profile extrusion line machines boast a range of additional benefits that make them the preferred choice for manufacturers worldwide. These include:
Safety Features: Our machines are equipped with advanced safety features, including emergency stop buttons, safety guards, and comprehensive safety protocols, ensuring the well-being of operators and minimizing the risk of accidents.
Energy Efficiency: With innovative energy-saving technologies and optimized hydraulic systems, our machines are designed to minimize energy consumption without compromising on performance, helping manufacturers reduce their carbon footprint and operating costs.
Technical Support: We provide comprehensive technical support and after-sales services to ensure seamless integration and optimal performance of our machines in your production facility. Our team of experienced technicians is available to address any inquiries or concerns you may have, providing peace of mind and confidence in your investment.
Customization Options: Recognizing that every manufacturing operation is unique, we offer customizable solutions tailored to your specific requirements. Whether you need specialized extrusion profiles, custom die designs, or integration with existing production lines, our team will work closely with you to deliver a solution that meets your exact needs and specifications.
Invest in the future of your manufacturing operation with our state-of-the-art aluminum profile extrusion line machines. Contact us today to learn more and take the first step towards achieving excellence in aluminum extrusion fabrication.
Why Choose Our Machine
When considering aluminium extrusion fabrication, choosing the right extrusion press is paramount to achieving optimal results. Our machine stands out for its unwavering commitment to quality, performance, and innovation. Here's why:
Proven Track Record: Backed by years of industry experience and a proven track record of excellence, our aluminium extrusion press is trusted by manufacturers worldwide.
Cutting-Edge Technology: Equipped with state-of-the-art technology and precision engineering, our machine offers unmatched levels of accuracy, efficiency, and reliability.
Customization Options: We understand that every project is unique, which is why our extrusion presses can be customized to meet specific production requirements, ensuring seamless integration into existing workflows.
Product Features
Precision Control: Advanced control systems allow for precise adjustment of parameters such as temperature, pressure, and speed, ensuring the production of high-quality extrusions.
Versatility: Aluminium extrusion presses can accommodate a wide range of dies, enabling the creation of diverse profiles tailored to specific customer requirements.
Efficiency: With rapid cycle times and minimal setup requirements, these presses offer exceptional efficiency, optimizing production processes and reducing operational costs.
Durability: Constructed from robust materials and designed for heavy-duty operation, aluminium extrusion presses boast longevity and reliability, ensuring uninterrupted production cycles.
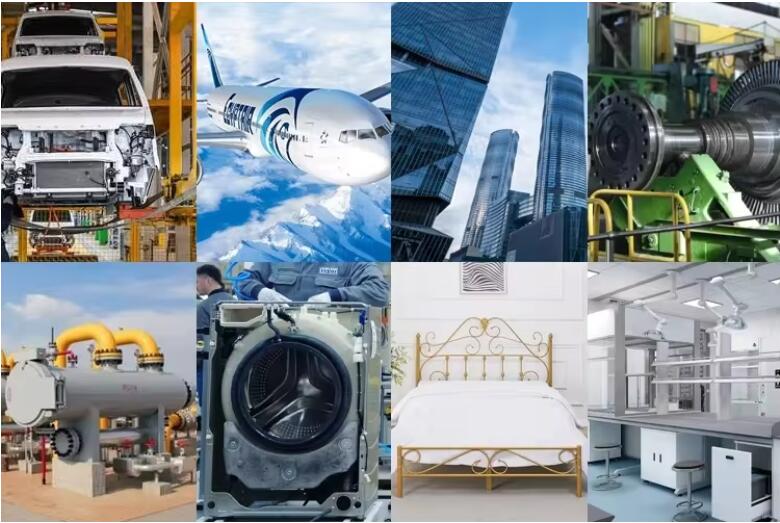
Automotive Industry
Application:
Production of lightweight and durable components such as frames, panels, and structural parts to improve fuel efficiency and performance.
Benefits:
Enhanced vehicle safety, reduced weight, and increased energy efficiency.
Aerospace Industry
Application:
Manufacturing of precision-engineered parts for aircraft, including fuselage sections, wing components, and interior structures.
Benefits:
High strength-to-weight ratio, corrosion resistance, and compliance with strict aerospace standards.
Construction Industry
Application:
Creation of building materials such as window frames, door frames, curtain walls, and structural supports.
Benefits:
Improved durability, energy efficiency, and aesthetic versatility.
Rail Transit
Application:
Fabrication of components for trains and rail infrastructure, including carriage bodies, interior fittings, and track elements.
Benefits:
Enhanced safety, reduced weight, and long-term durability under harsh conditions.
Electronics Industry
Application:
Production of heat sinks, casings, and structural parts for electronic devices and appliances.
Benefits:
Efficient heat dissipation, precision manufacturing, and lightweight construction.
Maritime Industry
Application:
Development of parts for ships and offshore structures, such as hull components, decking, and support frames.
Benefits:
Resistance to marine environments, reduced weight, and structural integrity.
Renewable Energy Sector
Application:
Manufacturing of components for solar panels, wind turbine structures, and other renewable energy systems.
Benefits:
High strength, lightweight properties, and corrosion resistance for outdoor use.
Industrial Machinery
Application:
Fabrication of parts for various industrial machines, including conveyor systems, automated equipment, and structural frameworks.
Benefits:
Precision engineering, robustness, and adaptability to different industrial applications.
Model | Unit | JY-630 | JY-800 | JY-1000 | JY-1250 | JY-1630 | JY-1800 | JY-2200 | JY-2500 |
Rated Extrusion Force | KN | 6300 | 8000 | 10000 | 12500 | 16300 | 18000 | 22000 | 25000 |
UST | 700 | 880 | 1100 | 1350 | 1800 | 2000 | 2420 | 2750 | |
Fixed Work Stress | MPa | 21 | 21 | 21 | 21 | 21 | 21 | 21 | 21 |
Locking Force | KN | 633 | 633 | 800 | 800 | 1586 | 1586 | 1586 | 1586 |
Perforation Force | KN | 1030 | 1030 | 1293 | 1293 | 2500 | 2800 | 3000 | 3500 |
(Double Action Extrusion Machine) | |||||||||
Extruding Speed | mm/s | 40 | 50 | 40 | 50 | 40 | 40 | 40 | 40 |
Extrusion Cylinder Preheating Power (Single Per Rod × Number) | KW | 1.2×12 | 1.5×12 | 2×12 | 2×12 | 3×12 | 3×12 | 3×15 | 3.5×15 |
Main Motor Power | KW | 75×3 | 132×3 | 132×3 | 132×4 | 132×5 | 132×6 | 132×7 | 132×8 |
Extrusion Barrel Inner Hole | mm | φ85-φ115×500 | φ105-φ135×550 | φ125-φ135×600 | φ135-φ165×650 | φ155-φ205×750 | φ175-φ225×800 | φ195-φ245×900 | φ205-φ265×1000 |
Size Range | |||||||||
(Aperture x Length) | |||||||||
Center Height of Main Unit | mm | 850 | 1040 | 1100 | 1180 | 1500 | 1500 | 1650 | 1850 |
Dimensions of Single-action Host (L × W × H) | m | 6.8×2.3×2.8 | 9.2×2.3×3.1 | 10×2.4×3.3 | 11.5×2.5×3.4 | 13.5×4.2×4.1 | 14.5×4.2×4.1 | 15.5×4.7×4.5 | 18×5×4.8 |
Dimensions of Dual-action Host (length × width × height) | m | 7.8×2.3×2.8 | 10.5×2.3×3.1 | 11.8×2.4×3.3 | 13.3×2.5×3.4 | 15.5×4.2×4.1 | 16.5×4.2×4.1 | 18.5×4.7×4.5 | 20×5×4.8 |
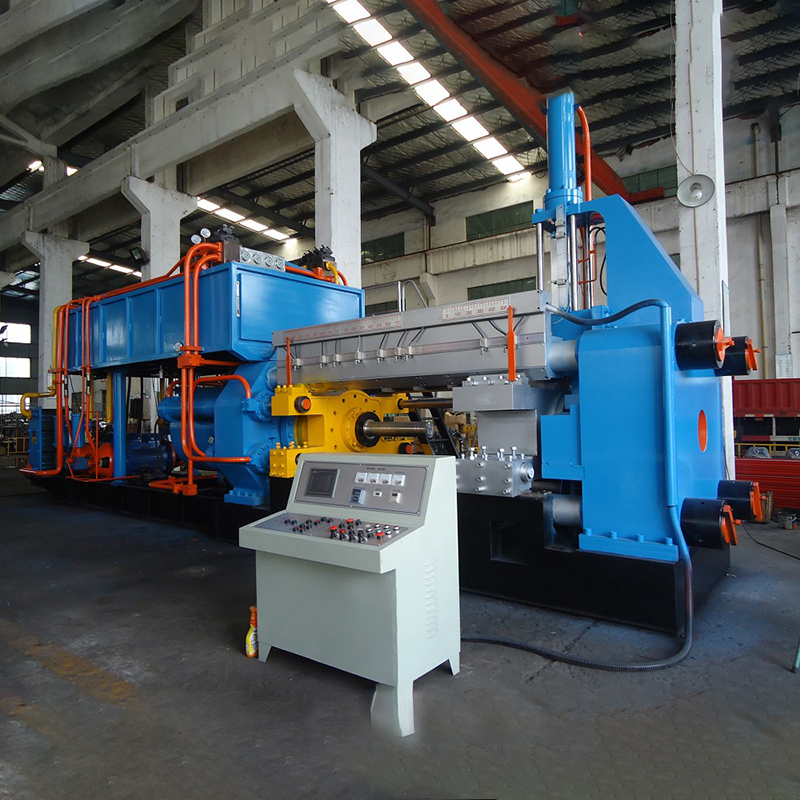
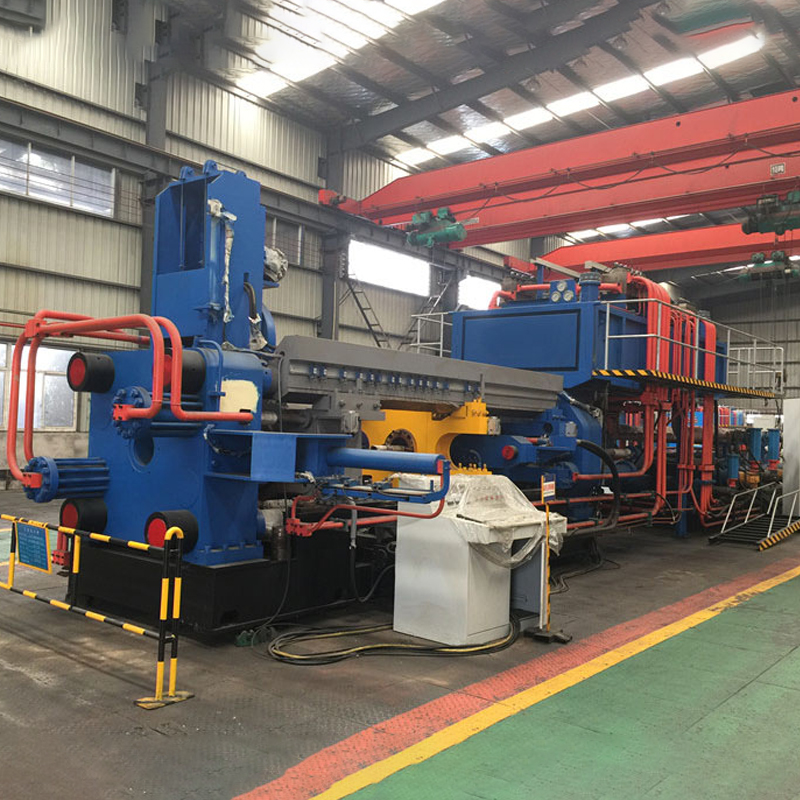
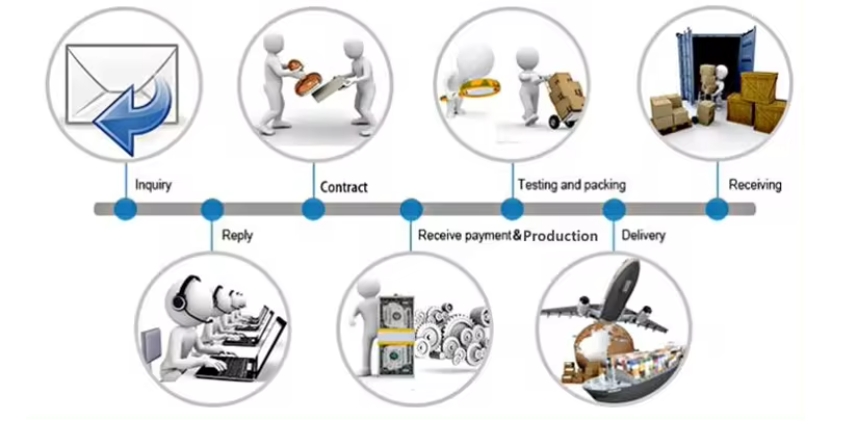
Whatsapp/Mob/Wechat: 008613394110095
Email: [email protected]
Website: www.aluextrusionpress.com
Inconsistent Extrusion Quality
Cause: Uneven heating, improper die alignment, or contaminated raw materials.
Solution:
Ensure uniform heating across the billet.
Regularly inspect and correctly align the die.
Use clean, high-quality raw materials.
Surface Defects on Extruded Profiles
Cause: Improper die design, inadequate lubrication, or debris in the die.
Solution:
Optimize die design for smooth material flow.
Apply adequate and appropriate lubrication.
Thoroughly clean the die before each use.
Extruder Jamming
Cause: Overloading, foreign materials in the feed, or inadequate cooling.
Solution:
Avoid overloading the extruder.
Ensure feed materials are free from foreign objects.
Maintain proper cooling systems.
Inconsistent Profile Dimensions
Cause: Fluctuations in extrusion pressure or temperature, or die wear.
Solution:
Monitor and maintain consistent extrusion pressure and temperature.
Regularly inspect dies for wear and replace them as needed.
High Scrap Rate
Cause: Incorrect machine settings, poor raw material quality, or operator error.
Solution:
Calibrate machine settings accurately.
Use high-quality raw materials.
Provide thorough training for operators.
Noisy Operation
Cause: Mechanical issues such as worn bearings or misalignment of components.
Solution:
Regularly inspect and replace worn bearings.
Ensure all machine components are properly aligned and lubricated.
Overheating of the Extruder
Cause: Insufficient cooling or excessive friction.
Solution:
Check and maintain cooling systems.
Apply proper lubrication to minimize friction.
Poor Surface Finish
Cause: Inadequate cooling, improper die design, or extrusion speed issues.
Solution:
Enhance cooling mechanisms.
Review and optimize die design.
Adjust extrusion speed for a smoother finish.
Material Flow Issues
Cause: Inconsistent material feed, improper die design, or blockage in the extrusion path.
Solution:
Ensure consistent material feed.
Optimize die design.
Regularly inspect and clear the extrusion path.
Difficulty in Die Changes
Cause: Improper handling or alignment issues during die installation.
Solution:
Follow proper procedures for die installation and removal.
Use alignment tools and techniques for precise die placement.
By addressing these common issues with proactive maintenance and proper operation practices, you can enhance the performance and longevity of your Aluminium Profile Extrusion Line Machines, ensuring efficient production and high-quality outputs.
Regular Cleaning
Action: Clean the machine thoroughly to remove any debris, dust, or leftover material.
Frequency: After each production run or shift.
Lubrication
Action: Apply appropriate lubricants to all moving parts to reduce friction and prevent wear.
Frequency: Daily or as specified by the manufacturer.
Inspection of Dies and Tools
Action: Inspect dies and tools for wear and damage, ensuring they are properly aligned and free of contaminants.
Frequency: Weekly, or more frequently if used intensively.
Cooling System Check
Action: Inspect and maintain the cooling system to ensure it is functioning properly and efficiently.
Frequency: Weekly.
Electrical System Maintenance
Action: Check electrical connections, wiring, and control panels for any signs of damage or wear.
Frequency: Monthly.
Hydraulic System Maintenance
Action: Inspect hydraulic systems for leaks, proper fluid levels, and component wear.
Frequency: Monthly.
Temperature and Pressure Calibration
Action: Regularly calibrate temperature and pressure settings to ensure they remain within the optimal range for your specific extrusion processes.
Frequency: Quarterly.
Bearing and Gear Maintenance
Action: Check and replace worn bearings and gears to prevent breakdowns and maintain smooth operation.
Frequency: Annually or as needed based on usage.
Software Updates
Action: Update the machine's software and control systems to the latest versions provided by the manufacturer.
Frequency: As updates become available.
Training for Operators
Action: Provide ongoing training for operators on best practices for machine operation and maintenance procedures.
Frequency: Regularly, especially when new systems or processes are introduced.
By following these maintenance steps, you can ensure the longevity, efficiency, and reliability of your aluminium profile extrusion line machines. Regular and proactive maintenance helps in minimizing downtime and maximizing production quality.
Q
What materials can be extruded using your machines?
A
Our extrusion machines are designed to extrude both aluminum and copper profiles and pipes, catering to a wide range of applications across various industries.
Q
What industries can benefit from your extrusion machines?
A
Our machines are used in the automotive, aerospace, construction, rail transit, electronics, maritime, renewable energy, and industrial machinery sectors, providing versatile and high-performance solutions.
Q
Can your machines be customized to specific production needs?
A
Yes, we offer robust R&D and product development capabilities to provide customized production services tailored to meet the unique needs of each customer.
Q
What are the benefits of using your extrusion machines?
A
Our machines offer advanced technology, high cost-performance ratio, precision engineering, and durability, ensuring efficient production processes and high-quality outputs.
Q
How do I ensure consistent extrusion quality?
A
To maintain consistent extrusion quality, ensure uniform heating, proper die alignment, and the use of clean, high-quality raw materials. Regular maintenance and calibration are also crucial.
Q
What kind of maintenance is required for your extrusion machines?
A
Regular cleaning, lubrication, inspection of dies and tools, checking cooling and hydraulic systems, calibrating temperature and pressure settings, and updating software are essential maintenance practices.
Q
What should I do if the extruder jams?
A
If the extruder jams, avoid overloading, ensure feed materials are free from foreign objects, and maintain proper cooling systems to prevent overheating.
Q
How can I prevent surface defects on extruded profiles?
A
To prevent surface defects, optimize die design, apply adequate lubrication, and ensure the die is clean and free of debris before use.
Q
What are the signs that the machine's bearings or gears need replacement?
A
Noisy operation, irregular motion, and decreased performance are signs that bearings or gears may be worn and need replacement. Regular inspection can help identify these issues early.
Q
Do you provide international support and service?
A
Yes, we have a global presence with clients in the US, Italy, Russia, and other countries. We offer comprehensive technical support and service to our international customers.
Q
What makes your extrusion machines stand out from competitors?
A
Our machines are distinguished by their advanced technology, high cost-performance ratio, and the ability to provide customized solutions. Additionally, our commitment to customer satisfaction and innovation sets us apart.
Q
How can I contact you for more information or support?
A
You can contact us through our website, email, or phone. Our customer service team is ready to assist you with any inquiries or support you may need.
Q
What information do I need to provide when ordering?
A
To ensure we meet your specific requirements, please provide details such as the type of materials you plan to extrude, the desired production capacity, any customization needs, and your industry application.
Q
Do you offer consultations before purchase?
A
Yes, we offer consultations to help you determine the best extrusion machine for your application. Our experts will assess your needs and recommend the most suitable equipment.
Q
What is the lead time for delivery?
A
Lead times vary depending on the machine model and any customizations required. Our sales team will provide an estimated delivery time when you place your order.
Q
What are the payment terms?
A
We offer flexible payment terms, which typically include an initial deposit with the balance due before shipment. Specific payment terms will be discussed and agreed upon during the ordering process.
Q
Do you provide financing options?
A
Yes, we offer financing options to qualified buyers. Our sales team can provide more details and assist you in arranging financing if needed.
Q
Is there a warranty on your Aluminium Profile Extrusion Line Machines?
A
Yes, all our extrusion machines come with a warranty. The warranty period and terms vary by model, and our sales team will provide detailed warranty information with your purchase.
Q
Do you offer training for operating the machines?
A
Yes, we provide comprehensive training for your operators to ensure they are proficient in using and maintaining the extrusion machines. Training can be conducted on-site or remotely, depending on your preference.
Q
What kind of after-sales support do you offer?
A
We offer robust after-sales support, including technical assistance, spare parts supply, and maintenance services. Our global support network ensures timely and effective service.
Q
Can I see a demonstration of the machine before purchasing?
A
Yes, we can arrange demonstrations either at our facility or through video conferencing. This allows you to see the machine in action and understand its capabilities.
Q
What customization options are available for Aluminium Profile Extrusion Line Machines?
A
We offer a wide range of customization options to meet your specific production needs, including custom die designs, specialized controls, and tailored machine configurations.
Q
How do you handle shipping and installation?
A
We manage shipping logistics to ensure safe and timely delivery of your machine. Our team can also assist with installation and commissioning at your site to ensure everything is set up correctly.
Q
Can I purchase spare parts and accessories for Aluminium Profile Extrusion Line Machines?
A
Yes, we offer a full range of spare parts and accessories for our extrusion machines. You can order these through our customer service team to ensure compatibility and performance.
Q
What should I do if I encounter issues after purchasing an Aluminium Profile Extrusion Line Machine?
A
If you experience any issues, please contact our customer service team. We provide prompt technical support and troubleshooting to resolve any problems you may face.