Photos of
Detailed introduction
О нас
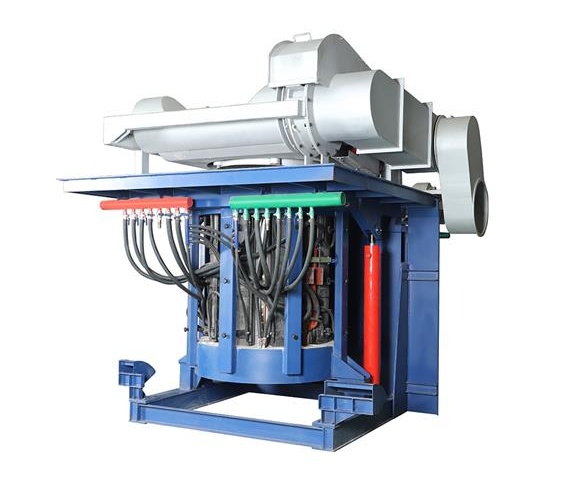
Dalian Jiuying Machinery Equipment Co., Ltd. is a leading manufacturer specializing in advanced induction melting technology, offering high-quality, efficient, and reliable equipment for metal melting and processing industries worldwide. With a commitment to innovation and customer satisfaction, we provide state-of-the-art solutions tailored to meet the diverse needs of our clients, ensuring superior performance and exceptional service.
The Medium Frequency Gold Induction Melting Furnace is an advanced piece of equipment designed for the efficient and precise melting of various metals, including gold, silver, platinum, copper, aluminum, and other materials with a melting point below 2000℃. This furnace combines cutting-edge technology with user-friendly features, making it ideal for industries such as jewelry manufacturing, precious metal refining, and more.
Working Principle
Working Principle
The Medium Frequency Gold Induction Melting Furnace operates based on electromagnetic induction, a process where an alternating current passes through an induction coil, creating a magnetic field. This magnetic field induces eddy currents within the metal placed in the crucible, generating heat due to the metal’s electrical resistance. The result is rapid and uniform heating, leading to efficient melting of the metal.
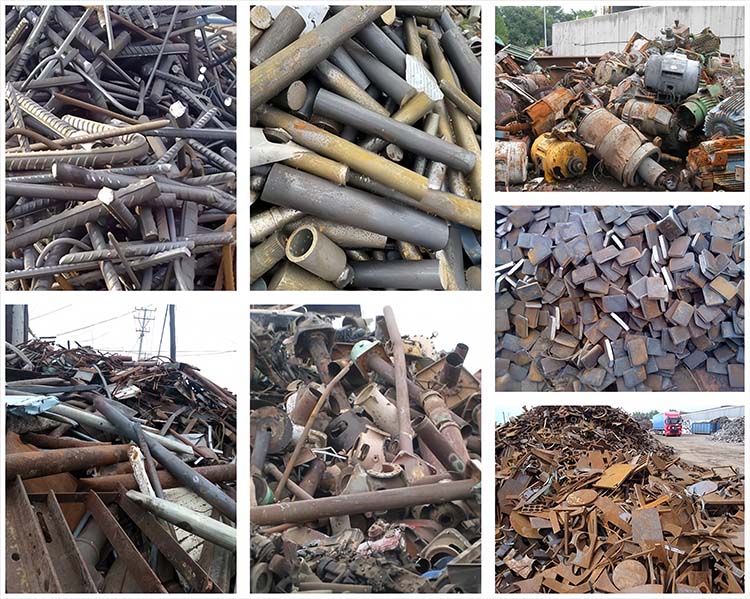
Key Steps in the Process
Key Steps in the Process
Induction Coil Activation: The power supply unit sends an alternating current to the induction coil.
Magnetic Field Generation: The alternating current generates a magnetic field around the coil.
Eddy Current Formation: The magnetic field induces eddy currents in the metal inside the crucible.
Heat Production: The eddy currents cause the metal to heat up due to electrical resistance.
Melting: The metal reaches its melting point and becomes a liquid, ready for further processing.
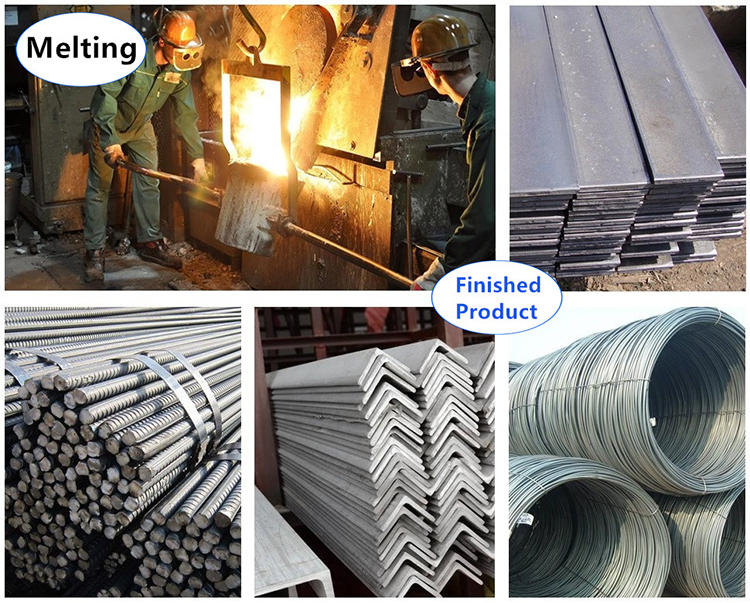
Product Features
Product Features
- Rapid Melting Speed: Capable of melting metals in under three minutes, with adjustable heating speeds to meet specific requirements.
- Uniform Temperature Distribution: Advanced electromagnetic induction technology ensures even heating and a consistent metal structure.
- Adjustable Power Output: Power settings ranging from 1KW to 10KW allow for various melting capacities and requirements.
- High Efficiency and Low Noise: The furnace features high heating efficiency, a water cooling system, and operates quietly.
- Energy Saving and Environmentally Friendly: With a thermal efficiency exceeding 95%, this furnace is a sustainable alternative to traditional fuel-based furnaces.
- Compact and Portable: The furnace is small, lightweight, and easy to move, requiring minimal installation and setup.
- High Maximum Temperature: Capable of reaching temperatures between 1500-2000℃, suitable for a wide range of metals.
- Safety Features: Equipped with over-temperature protection, water flow monitoring, and fault detection for safe operation.
1. Efficiency: The furnace’s rapid melting capabilities and high thermal efficiency translate to significant time and energy savings, boosting productivity.
2. Precision: Uniform temperature distribution ensures high-quality melts, essential for applications requiring exacting standards, such as jewelry manufacturing and metal refining.
3. Versatility: Suitable for a wide range of metals, including gold, silver, platinum, and copper, making it a versatile tool for various industries.
4. Ease of Use: The user-friendly control panel, minimal installation requirements, and comprehensive safety features make this furnace easy to operate and maintain.
5. Environmental Impact: With its high thermal efficiency and reduced reliance on fossil fuels, the furnace supports sustainable manufacturing practices.
How to Order
How to Order
To learn more about the Medium Frequency Gold Induction Melting Furnace or to request a quote, please contact us. Our team of experts is ready to provide you with detailed information and assist you in selecting the best furnace for your needs.
WhatsApp/WeChat: 008613394110095
Email: [email protected]
Website: www.aluextrusionpress.com
The Medium Frequency Gold Induction Melting Furnace is a versatile tool suitable for a variety of industries and applications. Its advanced technology and efficient performance make it ideal for the following uses:
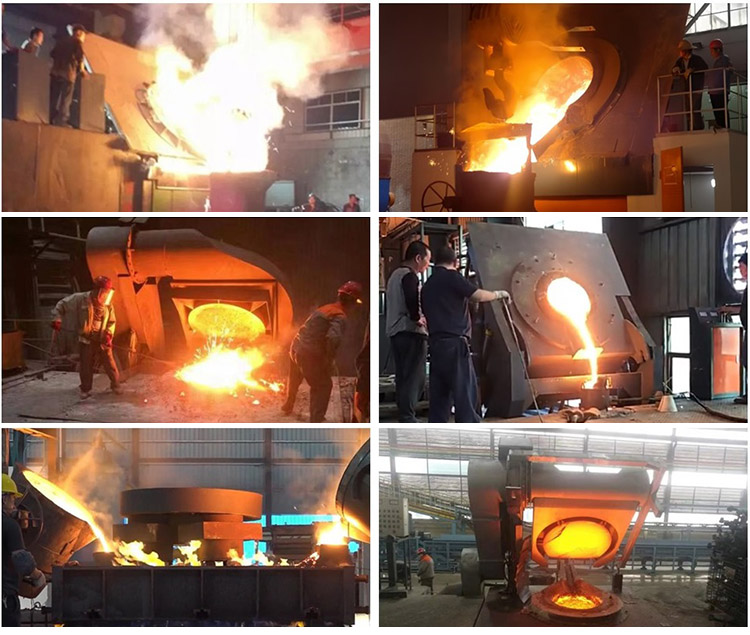
The Medium Frequency Gold Induction Melting Furnace is a versatile tool suitable for a variety of industries and applications. Its advanced technology and efficient performance make it ideal for the following uses: The furnace is perfect for melting precious metals such as gold, silver, and platinum to create intricate and high-quality jewelry designs. Its rapid and precise melting capabilities ensure that jewelers can produce detailed and flawless pieces. Refining companies benefit from the furnace’s ability to efficiently process raw metals into high-purity end products. The uniform heating and high thermal efficiency ensure that metals are melted and refined to the highest standards. Laboratories and research institutions use the furnace for experimenting with different metal alloys and developing new materials. The precise control over temperature and melting conditions makes it a valuable tool for scientific research and innovation. Dental labs utilize the furnace to melt metals for creating dental prosthetics, implants, and other dental devices. Its ability to achieve uniform temperature distribution ensures that the dental products are of the highest quality and durability. In the electronics industry, the furnace is used for melting metals required in the production of electronic components and assemblies. The precise melting process is crucial for manufacturing reliable and efficient electronic devices. Artists and sculptors use the furnace to melt metals for creating metal art and sculptures. Its ability to handle various metals and its precise control over the melting process allow artists to bring their creative visions to life. Metalworking shops and foundries benefit from the furnace’s ability to quickly melt and cast metals. Its flexibility and efficiency make it a valuable asset for producing metal parts and components. Various industrial manufacturing processes require the melting and casting of metals. The furnace’s high efficiency and precise control make it suitable for large-scale industrial applications, ensuring consistent and high-quality results. Technical schools and universities use the furnace for educational purposes, teaching students about metal melting processes and induction heating technology. Its user-friendly design and advanced features make it an excellent teaching tool.1. Jewelry Manufacturing
2. Precious Metal Refining
3. Research and Development
4. Dental Laboratories
5. Electronics Industry
6. Art and Sculpture
7. Metalworking and Foundries
8. Industrial Manufacturing
9. Educational Institutions
Melt Furnace Model | Power Control Cabinet | Furnace Body | Associated Transformer(KVA) | |||||||
(Aluminum Shell) | Power | Voltage | MF Voltage | Cabinet Size(mm) | Frequency | Weight | Furnace body Size(mm) | Induction Coil Inner Diameter | Weight | |
100kg | 100kw | 3×380v | 750v | 1000×800×1700 | 2500 | 0.5T | Φ630 | Φ300 | 0.3T | 125 |
250kg | 250kw | 3×380v | 750v | 1300×850×2000 | 1500 | 0.8T | Φ730 | Φ450 | 0.7T | 250 |
350kg | 350kw | 3×380v | 750v | 1300×850×2000 | 1500 | 0.8T | Φ730 | Φ580 | 0.9T | 400 |
500kg | 400kw | 3×380v | 1500v | 1300×850×2000 | 1000 | 1T | Φ1100 | Φ580 | 1T | 500 |
750kg | 600kw | 3×380v | 1500v | 1300×850×2000 | 1000 | 1T | Φ1100 | Φ580 | 1.2T | 630 |
1T | 800kw | 3×660v | 2400v | 1300×850×2000 | 1000 | 1.2T | Φ1180 | Φ720 | 1.3T | 900 |
1.5T | 1000kw | 3×660v | 2500v | 1300×850×2000 | 800 | 1.2T | Φ1250 | Φ760 | 1.8T | 1250 |
2T | 1500kw | 3×660v | 2500v | 2400×1000×2000 | 500 | 1.6T | Φ1350 | Φ860 | 2T | 1600 |
Melt Furnace Model | Power Control Cabinet | Furnace Body | Associated Transformer(KVA) | |||||||
(Steel Shell) | Power | Voltage | MF Voltage | Cabinet Size(mm) | Frequency | Weight | Induction Coil Inner Diameter | Weight | ||
0.25T | 350kw | 3×380v | 750v | 1500×850×2000 | 2000 | 1T | Φ450 | 0.7T | 315 | |
0.35T | 400kw | 3×380v | 750v | 1500×850×2000 | 1500 | 1.2T | Φ580 | 0.9T | 630 | |
0.5T | 600kw | 3×380v | 1500v | 2000×1300×2000 | 1000 | 1.8T | Φ580 | 1T | 800 | |
0.75T | 800kw | 3×380v | 1500v | 3500×1500×2000 | 1000 | 1.8T | Φ580 | 1.2T | 1000 | |
1T | 1200kw | 3×660v | 2400v | 4200×1500×2000 | 1000 | 2T | Φ720 | 1.3T | 1400 | |
1.5T | 1500kw | 3×660v | 2500v | 4200×1500×2000 | 800 | 2.2T | Φ760 | 1.8T | 1800 | |
2T | 2000kw | 3×660v | 2500v | 5300×1500×2000 | 500 | 2.5T | Φ860 | 2T | 2500 | |
3T | 2500kw | 3×660v | 3200v | 4200×1500×2200 | 500 | 3.5T | Φ980 | 2.5T | 3150 | |
5T | 3500kw | 3×660v | 3400v | 5500×1800×2200 | 500 | 4.5T | Φ1140 | 4.5T | 4000 | |
10T | 7000kw | 3×660v | 3700v | 6800×1800×2000 | 300 | 6T | Φ1450 | 2.3T | 8000 |
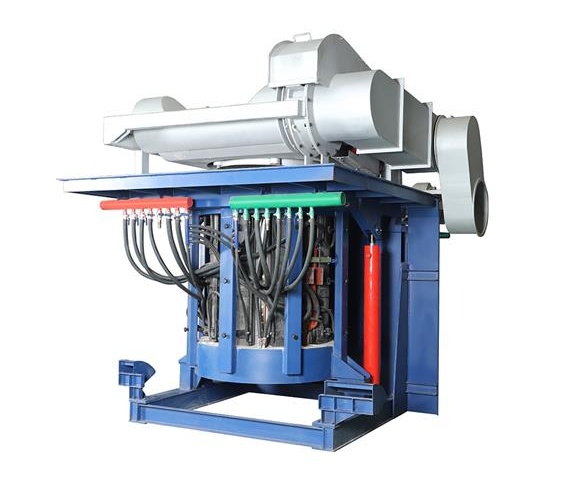
Induction Steel Melting Furnace
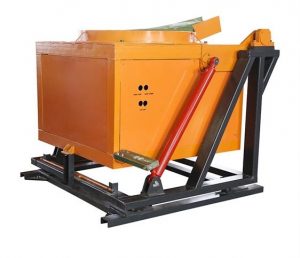
Aluminum Melting Furnace
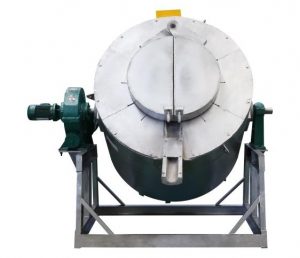
Copper Melting Furnace
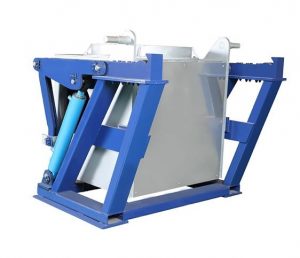
Stainless Steel Melting Furnace
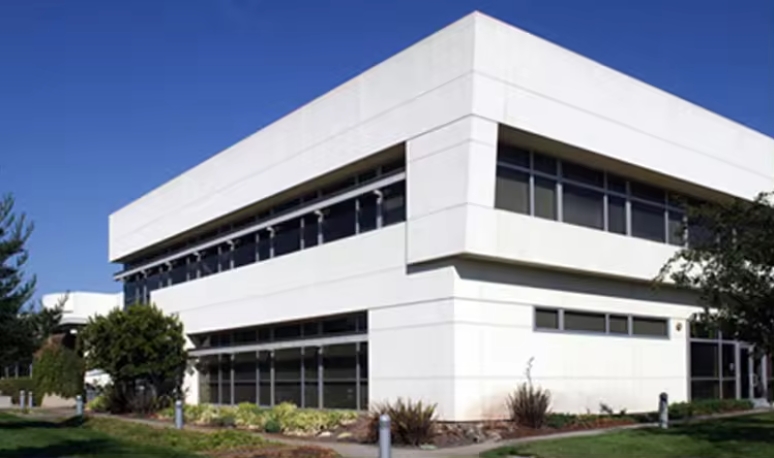
Dalian Jiuying Machinery Equipment Co., Ltd. is a renowned manufacturer dedicated to the innovation, research, and production of premium extrusion machinery. Founded in 2015, we have rapidly grown to become a trusted provider of cutting-edge solutions for customers across the globe. Our commitment to quality and excellence drives us to continually improve our products and services, ensuring we meet the evolving needs of our clients. Whether it's for industrial, commercial, or specialized applications, Dalian Jiuying Machinery Equipment Co., Ltd. is your reliable partner in achieving superior performance and efficiency.
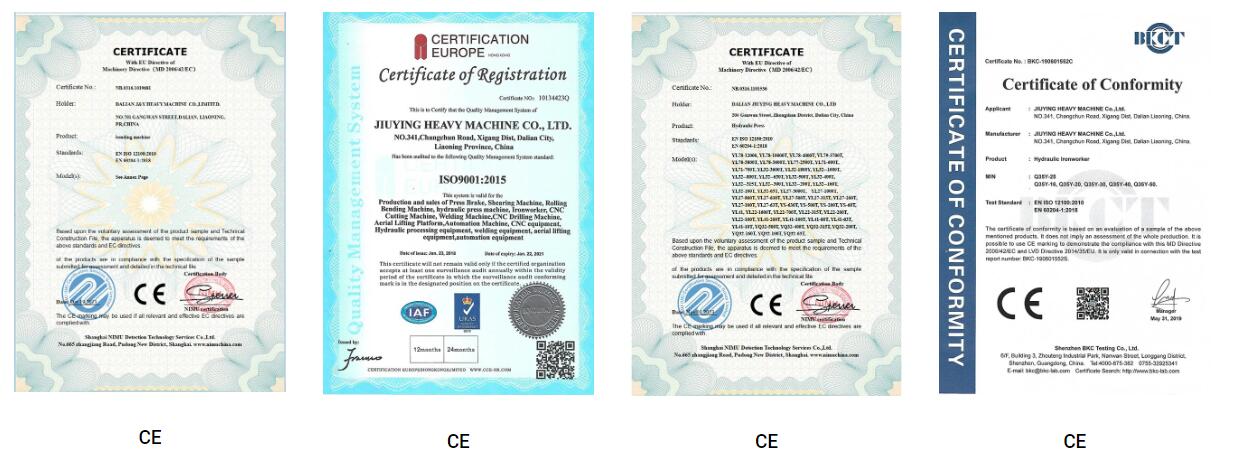
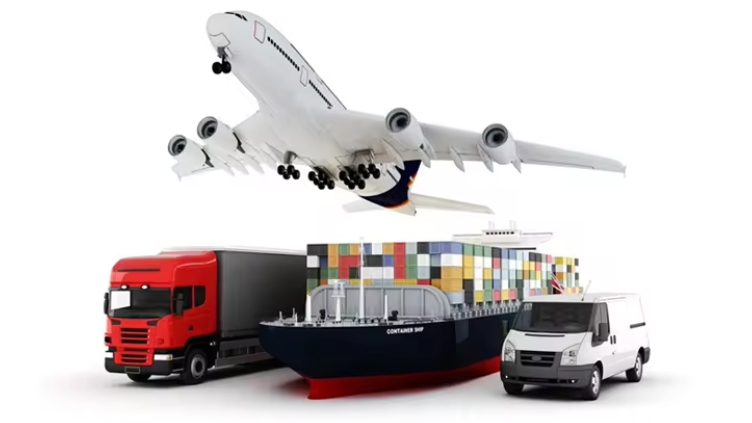
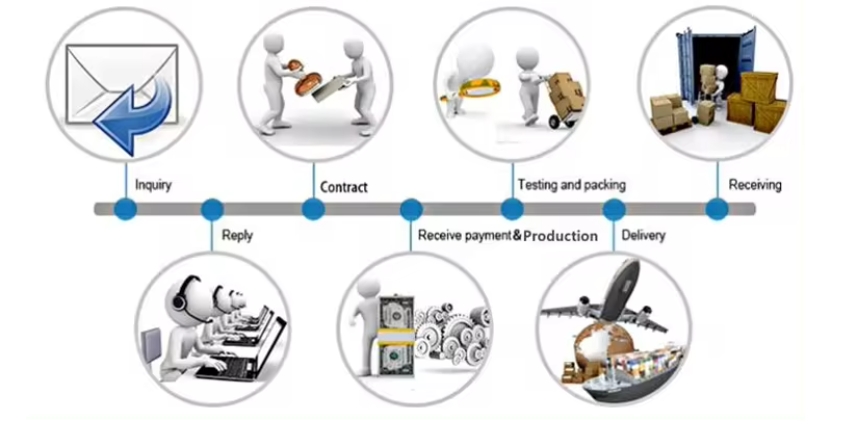
Whatsapp/Mob/Wechat: 008613394110095
Email: [email protected]
Website: www.aluextrusionpress.com
Operating an Induction Steel Melting Furnace efficiently requires understanding and addressing common issues that may arise during its use. Here are some typical problems and their solutions:
Issue 1: Inconsistent Heating or Melting
Symptoms: Uneven heating of metals, delays in melting, or failure to reach desired temperatures.
Possible Causes and Solutions:
Improper Coil Alignment: Ensure the induction coil is properly aligned with the crucible to maximize heating efficiency. Adjust the coil if necessary.
Metal Placement: Verify that metals are correctly positioned inside the crucible. Ensure metals are evenly distributed for uniform heating.
Power Supply Issues: Check the power supply unit for any fluctuations or irregularities. Ensure the furnace is receiving adequate power within the recommended specifications.
Cooling System Malfunction: Inspect the water cooling system to ensure it is functioning correctly. Overheating can affect the furnace's performance.
Issue 2: Overheating
Symptoms: Excessive heat levels leading to furnace shutdowns or safety alarms.
Possible Causes and Solutions:
Cooling System Failure: Check for blockages in the water lines or insufficient water flow. Clean or replace filters and ensure proper coolant circulation.
Improper Cooling Settings: Adjust the cooling system settings to maintain optimal temperature levels during operation.
Crucible Overloading: Avoid overloading the crucible beyond its capacity, as this can lead to overheating. Follow manufacturer guidelines for maximum load capacities.
Issue 3: Electrical Faults or System Errors
Symptoms: Error codes displayed on the control panel, unexpected shutdowns, or electrical malfunctions.
Possible Causes and Solutions:
Faulty Connections: Inspect all electrical connections and terminals for loose connections or corrosion. Tighten connections as needed.
Power Supply Issues: Check for fluctuations in voltage or current. Ensure the power supply unit is functioning correctly and within operational parameters.
Sensor Calibration: Verify the calibration of temperature sensors and other monitoring devices. Recalibrate sensors if readings are inaccurate.
Software/Firmware Updates: Ensure the furnace's software and firmware are up-to-date to resolve potential bugs or system errors.
Issue 4: Poor Crucible Performance
Symptoms: Cracks, erosion, or premature wear of the crucible affecting melting efficiency.
Possible Causes and Solutions:
Crucible Quality: Use high-quality crucibles suitable for the metals being melted. Inspect crucibles regularly for signs of wear and replace as needed.
Proper Handling: Avoid sudden temperature changes or thermal shocks that can weaken crucible integrity.
Maintenance Practices: Clean crucibles thoroughly and maintain them according to manufacturer guidelines. Use appropriate cleaning agents to remove metal residues.
Issue 5: Noise or Vibration
Symptoms: Excessive noise or vibration during furnace operation.
Possible Causes and Solutions:
Mechanical Issues: Check for loose components, worn bearings, or misaligned parts causing vibration. Tighten or replace components as necessary.
Cooling System: Ensure the water cooling system is functioning correctly to prevent overheating, which can lead to noisy operation.
Environmental Factors: Consider environmental factors such as foundation stability or acoustic insulation to mitigate noise and vibration.
Issue 6: Safety Alarms or Emergency Shutdowns
Symptoms: Emergency stops or safety alarms triggered during operation.
Possible Causes and Solutions:
Over-temperature Protection: Monitor temperature settings and adjust safety thresholds if necessary. Ensure sensors are accurate and responsive.
Leakage Detection: Address any leaks in the furnace or cooling system promptly to prevent safety alarms.
System Checks: Regularly test emergency stop functions and safety features to ensure they operate correctly in case of emergencies.
Additional Tips:
Regular Maintenance: Implement a scheduled maintenance program to address issues proactively and prevent downtime.
Operator Training: Ensure operators are trained in proper furnace operation, maintenance procedures, and troubleshooting techniques.
Consult Manufacturer: For complex issues or persistent problems, consult the furnace manufacturer or technical support for specialized assistance.
Proper maintenance of the Induction Steel Melting Furnace is crucial to ensure its optimal performance, longevity, and safety. Regular maintenance helps prevent unexpected downtime and costly repairs. Below are detailed guidelines for maintaining your induction steel melting furnace:
Daily Maintenance
Visual Inspection:
- Examine the induction coil, crucible, and power supply unit for any visible damage or wear.
- Check all connections to ensure they are secure and free from overheating or loose wires.
Cleaning:
- Remove any metal splashes or debris from the furnace area to prevent contamination and ensure efficient operation.
- Clean the exterior of the furnace to keep it free from dust and dirt.
Cooling System Check:
- Verify that the water cooling system is working correctly.
- Ensure that the water flow is adequate and there are no leaks in the hoses or connections.
Weekly Maintenance
Electrical Component Inspection:
- Inspect the power supply and control panel for any signs of wear or damage.
- Ensure all electrical connections are tight and secure.
Safety Feature Testing:
- Test all safety features, such as over-temperature protection and fault detection systems.
- Confirm the functionality of the emergency stop function.
Performance Review:
- Monitor the furnace’s performance during operation, focusing on heating times and temperature uniformity.
- Address any irregularities or performance issues promptly.
Monthly Maintenance
Deep Cleaning:
- Perform a thorough cleaning of the induction coil and crucible to remove any metal residue buildup.
- Use appropriate cleaning agents and tools to avoid damaging components.
Crucible Inspection and Replacement:
- Check the crucible for cracks, erosion, or other signs of wear.
- Replace the crucible if necessary to maintain efficient melting operations.
Lubrication:
- Lubricate moving parts, such as tilting mechanisms and door hinges, to ensure smooth operation.
- Use manufacturer-recommended lubricants to avoid damage.
Annual Maintenance
Professional Inspection:
- Schedule a comprehensive inspection by a qualified technician to check all components thoroughly.
- Have the technician calibrate the furnace for optimal performance.
Software and Firmware Updates:
- Update the furnace’s software and firmware to the latest versions for new features and improvements.
- Ensure that all updates are compatible with your existing system.
Usage Log Review:
- Analyze the furnace’s usage logs to identify patterns of wear or recurring issues.
- Use this information to adjust maintenance routines and improve performance.
Troubleshooting Common Issues
Inconsistent Heating:
- Check for proper coil alignment and correct placement of the metal in the crucible.
- Inspect the power supply and connections for faults.
Overheating:
- Ensure the cooling system functions correctly and there are no obstructions in the water flow.
- Verify that temperature sensors are accurate and properly calibrated.
Unexpected Shutdowns:
- Inspect all electrical connections and components for signs of damage or wear.
- Check for error codes on the control panel and refer to the user manual for troubleshooting steps.
Additional Tips
- Training: Ensure all operators are adequately trained on furnace operation and maintenance procedures.
- Spare Parts: Keep an inventory of critical spare parts to minimize downtime in case of component failure.
- Documentation: Maintain detailed records of all maintenance activities, inspections, and repairs for future reference and compliance with safety regulations.
Q1: What types of metals can the Induction Steel Melting Furnace handle?
A1: The Induction Steel Melting Furnace is capable of melting a variety of metals including steel, iron, copper, aluminum, and other metal materials with melting points below 2000°C.
Q2: How long does it take to melt steel using the furnace?
A2: The melting time varies depending on the amount and type of metal, but typically, the furnace can melt steel within 40-60 minutes per batch.
Q3: What are the power requirements for the furnace?
A3: The power requirements can vary based on the model, but generally, the furnace operates within a range of 1KW to 10KW. Detailed power specifications should be checked in the user manual or product specifications.
Q4: Is the furnace energy-efficient?
A4: Yes, the Induction Steel Melting Furnace boasts high thermal efficiency, often exceeding 95%. It is designed to be energy-saving and environmentally friendly.
Q5: What safety features are included with the furnace?
A5: The furnace is equipped with multiple safety features including over-temperature protection, water flow monitoring, fault detection systems, and an emergency stop function. It also has a leakage furnace alarm and a smelting management system.
Q6: How do I maintain the furnace to ensure its longevity?
A6: Regular maintenance is crucial. Daily tasks include visual inspections and cleaning. Weekly, you should inspect electrical components and test safety features. Monthly, perform deep cleaning and lubricate moving parts. Annually, schedule a professional inspection and update the software/firmware. Detailed maintenance guidelines can be found in the user manual.
Q7: Can the furnace be used continuously?
A7: Yes, the furnace is designed to operate continuously for 24 hours, making it suitable for high-demand industrial applications.
Q8: What cooling system does the furnace use?
A8: The furnace uses a water cooling system to manage heat generated during the melting process. Ensuring the cooling system is functioning correctly is vital for safe and efficient operation.
Q9: Is the furnace easy to install and operate?
A9: Yes, the furnace is designed for ease of installation and operation. It requires minimal setup and comes with a user-friendly control panel. Detailed installation instructions and operational guidelines are provided in the user manual.
Q10: What kind of after-sales support is available?
A10: Dalian Jiuying Machinery Equipment Co., Ltd. offers comprehensive after-sales support, including technical assistance, maintenance services, and spare parts availability. For specific issues or inquiries, you can contact our support team directly.
Q11: How do I troubleshoot common issues with the furnace?
A11: Common issues can often be resolved by checking connections, ensuring the cooling system is functioning, and inspecting components for damage. The user manual provides a troubleshooting section with detailed steps for addressing various problems. If issues persist, contact our technical support team for assistance.
Q12: Can the furnace be customized for specific needs?
A12: Yes, customization options are available to meet specific requirements, including adjustments to the induction coil design and power output. Contact our sales team to discuss your specific needs.
Q13: What are the dimensions and weight of the furnace?
A13: The dimensions and weight vary depending on the model and capacity of the furnace. Detailed specifications can be found in the product datasheet or by contacting our sales team for more information.